Porsche’s Leipzig Plant: New Standard for EV Manufacturing
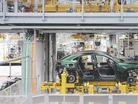
Porsche's Leipzig plant has set a new standard for flexibility in automotive production, emerging as a model of how established carmakers can adapt to the EV era.
By enabling the production of multiple powertrains—including fully electric, hybrid and combustion vehicles—on a single assembly line, Porsche highlights the adaptability and innovation required to keep pace with the evolving demands of the automotive industry.
Flexible manufacturing for an electrified future
As the automotive sector undergoes a significant transition toward electrification, Porsche's approach at Leipzig highlights the potential for traditional automakers to blend EV production into existing facilities efficiently.
Handling diverse powertrain types on one line is critical as manufacturers aim to meet the shifting market demand for EVs.
The plant's capacity to produce the all-electric Macan alongside hybrid and gasoline-powered models exemplifies the convergence of different drive technologies, which is increasingly shaping the EV industry.
By refining their production processes, manufacturers like Porsche are reducing costs and positioning themselves to scale EV production seamlessly.
Innovative assembly processes address unique EV challenges
One of the most challenging aspects of integrating EVs into traditional production lines is managing the "marriage" process, where the powertrain is joined with the vehicle body. The process is particularly intricate for EVs due to their unique components, such as large battery packs and electric motors.
Sebastian Böttcher, Head Engineer at Leipzig, explained the learning curve Porsche encountered, stating:
"An additional type of powertrain is like a little world of its own, with new requirements, special procedures, and special tools. We had much learning to do."
Porsche's focus on overcoming these challenges highlights the complexities of EV manufacturing as companies adapt traditional assembly procedures to suit the needs of modern electric drivetrains.
Advanced automation and quality control for EV precision
Porsche has implemented a range of advanced automation and quality control technologies at its Leipzig plant to support precise EV manufacturing. These include:
- Automatic Screw Leading Systems: Ensures the accurate placement and tightening of screws, which is essential for high-voltage components.
- Camera Systems for Battery Inspection: Automated cameras inspect batteries to ensure they meet rigorous safety and performance standards.
- Automated Measuring for Screw Spindle Evaluation: Provides detailed assessments of each screw spindle, helping ensure consistent quality throughout the assembly.
The systems address the specific demands of EV production, where precision is paramount for safety and performance, particularly when handling high-voltage components.
Scalability and production efficiency at Leipzig
Porsche's Leipzig facility can produce approximately 600 vehicles daily, including EVs, demonstrating the plant's high-volume production potential. The capacity is crucial as the EV market scales to meet growing consumer demand and aims to reach production volumes that rival traditional vehicles.
Sebastian adds, "We have created a highly productive system which has been seamlessly incorporated into all the plant workflows."
The seamless integration is a testament to the plant's design and operational efficiency, showing how traditional manufacturing ecosystems can support EV production without compromising productivity.
Commitment to continuous improvement
The Leipzig plant's ongoing optimisation reflects Porsche's commitment to staying ahead of the curve in an industry characterised by rapid technological advancements.
"There's obviously always things that need optimising, but that's standard procedure for us at Porsche."
Porsche's focus on overcoming these challenges highlights the complexities of EV manufacturing as companies adapt traditional assembly procedures to suit the needs of modern electric drivetrains.
Advanced automation and quality control for EV precision
Porsche has implemented a range of advanced automation and quality control technologies at its Leipzig plant to support precise EV manufacturing. These include:
- Automatic Screw Leading Systems: Ensures the accurate placement and tightening of screws, which is essential for high-voltage components.
- Camera Systems for Battery Inspection: Automated cameras inspect batteries to ensure they meet rigorous safety and performance standards.
- Automated Measuring for Screw Spindle Evaluation: Provides detailed assessments of each screw spindle, helping ensure consistent quality throughout the assembly.
The systems address the specific demands of EV production, where precision is paramount for safety and performance, particularly when handling high-voltage components.
The dedication to improvement aligns with the rapid pace of EV technology and manufacturing innovation, ensuring that Porsche's facilities remain adaptable as the market continues to evolve.
Setting a new standard in EV manufacturing
Porsche's Leipzig plant models how traditional automakers can successfully incorporate EV production into their operations without sacrificing flexibility or efficiency. By creating a versatile manufacturing process capable of handling multiple drive types, Porsche is paving the way for the future of EV production.
The approach is likely to become increasingly important as the automotive industry continues its shift toward electrification, with flexible production facilities like Leipzig poised to lead the charge.
Make sure you check out the latest edition of EV Magazine and also sign up to our global conference series - Sustainability LIVE 2025.
EV Magazine is a BizClik brand.