A safety critical approach, driven by EVs’ ‘hidden hero’
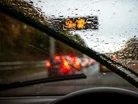
On the surface of the automotive industry, it’s somewhat difficult to understand how much things have evolved since the dawn of EVs. Looking from the outside in, we often see them as the electrified counterparts to their ICE predecessors. But, there is so much more to it than that.
A whole new architecture—this is what drives EVs and enables higher speeds, increases in efficiency and improvements in safety. In order to keep drivers and the general public safe, organisations must apply the lessons they’ve learned, to ensure that EVs meet rigorous standards and integrate with other digitally-driven solutions.
The EVs of today are backed by a global testbed of electric propulsion performance, with motorsport—and even aerospace—sharing applications and innovations scaled to meet safety requirements on public highways.
To share a great example of how industry lessons are carried into the commercial market, McLaren Applied’s Head of Electrification, Stephen Lambert, explains how its inverter technologies translate from aerospace and motorsport to the wider manufacturing of all-electric vehicles.
“We’ve developed a lot of our solutions around safety critical systems and products, which then evolved as automotive became more interested in safety engineering,” says Lambert.
Such competencies filtered into one of the key products that McLaren Applied supplies to the industry today—its electrical inverters—which Lambert claims to be the “hidden hero” at the heart of every EV. But, the inverter plays much more of a role than simply converting and carrying current between the electrical systems of electric cars. It is also incorporated into safety state mechanisms that allow them to protect cars and drivers in the event of malfunction.
“The inverter is kind of the heart, the hidden hero within the EV drivetrain. It takes the DC power from the battery and converts it to AC for the motor, but it's really the core part of the drivetrain,” says Lambert. “It takes all the signals from the driver and turns them into actions for the car, but is also responsible for the safety critical aspects of that vehicle as well.”
Also EVs may seem far from the complexity of aviation electronics, the principles are the same. The ‘safe state’ referred to by Lambert is an innovation that is further enabled by the same equipment that ensures electrified cars are able to move.
Electric vehicles open up new safety capacity
The differing architecture between ICE and EV presents only opportunities for OEMs, as they look to make their cars safer for drivers. The inverter being a key component of this, as explained by Lambert, individual drive for each wheel of the electric car eliminates the need for the ‘safe state’ expected in aerospace.
“If there is a problem, you need the ability to go into a safe state. That’s usually if there’s a problem with a vehicle,” says Lambert.
What this means is, “you turn off the drivetrain and can coast to a safe stop—this is one of the differences we’ve found compared to aerospace safety systems where you don’t create a safe state in the same way.”
Although the safe state idea is something unique to vehicles on public roads, the applications from motorsport come from an opposite application, whereby the teams “learn how to best use the technology, how to push them to their limits before they can fail, where that failure point is, and how we get the most out of that, the asset that is the inverter.”
Understanding how to control the component that manages the energy flow within an EV is what sets them apart from their ICE counterparts. As we see more autonomous driving capabilities appearing industry wide, the combination of automation and advanced inverter technologies will enable OEMs to make cars that are built to react to incidents on the road, but act accordingly, leveraging a more controllable system in the process.
“The EV world and the autonomy world are going to come together at some point,” says Lambert. “This means making sure that EVs have a system for taking over the drivetrain. So, in the case of a failure in the autonomous controller stack, they can take control of the vehicle and automate a safe stop.”
Maximum safety is key for OEMs, but to really understand how they achieve this, they must first understand the regulations at play. Enabling safety in wave two of the overall electrification of vehicles will allow them to progress further, where the third wave is all about increasing efficiency and reducing the cost and energy consumption.
“In wave three of electrification, it’s all about efficiency. We believe that, when you start looking at efficiency, you enter a virtuous cycle. As you make your drivetrain more efficient, you can reduce your battery size while achieving the same range, as well as the weight of the vehicle.”
- Parkopedia Provides Enhanced Charging Solutions to BMW GroupTechnology
- How Gotion High-tech is Revolutionising Battery TechnologiesCharging & Infrastructure
- Hybrid Airlander 10 to fly across Scottish HighlandsFleet & Commercial
- Ready for Tesla's Autonomy Investor Day & Driverless EVsSelf Drive