Addressing Range Anxiety and Cost Challenges in BEV Adoption
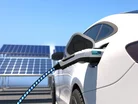
Battery Electric Vehicles (BEVs) deliver a smooth and powerful driving experience with lower emissions. Yet two limitations continue to impact conversion from traditional combustion engines to BEV vehicles – range anxiety and cost to purchase.
Timothy Gotsick, VP Technology & Innovation, MacDermid Enthone Industrial Solutions, tells us why he thinks BEVs are the future and how the EV sector can address these two issues.
Addressing range anxiety
Gotsick suggests that range anxiety can be addressed in two ways – give BEVs more range or make them incredibly easy to ‘refuel’.
“Adding more range to a BEV means increasing the batteries (which adds cost and weight) or more electrical efficiency. Improved efficiency not only increases range, but can also attack buyers' inherent cost concerns,” Gotsick says.
MacDermid Enthone Industrial Solutions is working with EV engineers to increase the electrical and thermal efficiency of every part in the car by providing low resistance coatings, highly efficient heat paths to manage the temperature of all operating components and enabling the use of lighter parts by better protecting them from the environment.
“Efficient battery use may delay the need for charging, but how do we efficiently and reliably enhance the BEV charging experience? The answer lies in producing a large number of readily available charging stations that are reliable and redundant,” says Gotsick. “As providers of chemistry that help protect almost any industrial component you can imagine, we want to play a big role in making sure no charging station fails because it is damaged by the effects of time and weather.”
The average age of cars on the road in the US today now exceeds 12 years. Gotsick argues that if EV manufacturers can make the engines, suspension, wheels and fasteners which hold cars together last over a decade, the company will be well positioned to make the parts in a stationary charging station hold up to even the harshest environments.
“Along with reliability, we need to improve charging speed. The high current needed for fast charging can cause heat to build up in batteries and the BMS (battery management system),” he says. “Working together with our colleagues at MacDermid Alpha Assembly Solutions, we are creating special combinations of materials that make it easier for heat to be removed from those components, enabling higher charging currents and allowing BEVs to spend more time on the road than at the charger.”
Soaring investments in domestic battery manufacturing
Until now, BEVs have cost more than equivalent internal combustion vehicles. Early adopters of BEVs have paved the way for EV automakers to increase production volumes to a level where economies of scale become meaningful. Tesla made 1.8m BEVs in 2023, compared to the less than 50,000 sold in 2015, meanwhile BYD made 1.5m.
“Though still very early in their technology development and adoption curve, this incremental growth is enabling BEV performance and cost to improve much faster than conventional cars,” says Gotsick. “Investments in domestic battery manufacturing in the US, along with market competition by a wide array of suppliers, are driving down the cost of components while OEMs are figuring out ways to design cost out of their cars.”
The combination of volume, experience and competition positions automakers to bring the cost of BEVs to very competitive levels.
*******************
Make sure you check out the latest edition of EV Magazine and also sign up to our global conference series - Sustainability LIVE 2024.
*******************
EV is a BizClik brand.