JLR: Sustainability with Closed-Loop Seat Foam Recycling
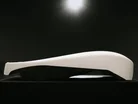
JLR has achieved a significant milestone in sustainability by successfully integrating recycled polyurethane seat foam from used vehicles into new seat production.
The technical breakthrough, achieved in collaboration with Dow's MobilityScience and global seating leader Adient, marks the first successful application of closed-loop seat foam recycling in automotive manufacturing.
Polyurethane foams, designed for durability, have historically posed significant recycling challenges, often ending up in landfills for generations.
JLR's closed-loop process aims to tackle this issue, creating a sustainable supply chain that reduces emissions, eliminates waste and secures a low-carbon alternative for seat foam in its vehicles.
The new seat foam is projected to halve CO2e emissions per seat while maintaining premium performance standards. The innovation is estimated to avoid more than 44kg of CO2e per seat, the equivalent of charging nearly 3,000 smartphones.
Andrea Debbane, Chief Sustainability Officer at JLR, emphasises the importance of collaboration in achieving these milestones: "This represents a collective commitment to doing things differently, challenging us to rethink our approach from all angles.
"The knowledge and applications demonstrate that full circularity is feasible and critical to our transition."
Industry collaboration: A formula for success
The breakthrough comes as a result of a groundbreaking collaboration between JLR, Dow and Adient.
Through its RENUVA programme, Dow developed advanced depolymerisation technologies to convert end-of-life waste into new circular materials.
Jon Penrice, Mobility President at Dow, highlights the partnership's importance: "By leveraging recycled polyurethane, we are developing technologies that support net-zero goals and maintain the superior comfort and quality of JLR seats."
Adient, meanwhile, was crucial in incorporating closed-loop materials into seating solutions.
Mick Flanagan, Vice President of the Customer Group at Adient, remarks: "This collaboration demonstrates how innovative partnerships can drive significant advancements in the automotive industry while ensuring luxury and comfort for our customers."
Driving change through JLR's circularity lab
JLR's Circularity Lab in Gaydon is at the heart of this innovation, serving as a hub for sustainability research and testing. Teams disassemble vehicles to identify opportunities for material reuse and recycling, feeding data directly into early decision-making for new vehicle development.
Historically, vehicle design has prioritised performance and aesthetics over end-of-life recyclability. Mixed materials, adhesives and complex fixing methods often made recycling nearly impossible. The Circularity Lab tackles these challenges through a collaborative "learn-through-doing" approach.
For example, research on front bumpers revealed that reducing the number of polymers could save 177,500 kg CO2e over a single model line while cutting costs by US$700,000.
JLR's latest success builds on its award-winning aluminium recycling project, which recycled post-industrial waste into new body panels. The initiative, driven by supply chain collaboration, developed a new aluminium grade optimised for closed-loop recycling processes.
Supporting the Reimagine strategy
JLR's commitment to circular economy principles is central to its Reimagine strategy, which aims to redefine sustainability benchmarks in the automotive industry. The vision extends to its industrial transformation, including refurbishing equipment to balance capability, energy efficiency and CO2e impact in preparation for an all-electric future.
As an Ellen MacArthur Foundation Network Partner since 2023, JLR applies circular economy principles to all aspects of its business, reinforcing its leadership in sustainable innovation.
By creating closed-loop solutions for materials like polyurethane foam, JLR is reducing waste and emissions and setting the stage for a more resource-efficient automotive industry.
Explore the latest edition of EV Magazine and be part of the conversation at our global conference series, Sustainability LIVE and Manufacturing LIVE.
Discover all our upcoming events and secure your tickets today.
EV Magazine is a BizClik brand