EV Batteries: Supply Chain & Sustainability Challenges
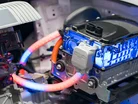
The drivers of the world face a dilemma, in balancing the need for EV batteries to be affordable and also ethically sourced.
With projected EV sales forecast to grow by tens of millions of vehicles by 2030, the demand for minerals and elements such as lithium, copper and nickel is going to be extremely challenging to reach. According to recent figures from intelligence specialist S&P Global, by 2030 the market demand for lithium-ion batteries for light vehicles will hit around 3.4 Terawatt hours (TWh) annually. However, the current output for the auto industry is just 0.30 TWh.
As S&P Global points out, even if fresh lithium reserves were to be discovered, it takes at least 15 to 20 years to develop an operating mine from the time of discovery. It also says that currently there is a lack of tracing and transparency around the sourcing of battery metals.
It seems that, while industry is becoming adept at tracking emissions of invisible gases, it is less far well-placed to track ESG violations - such as forced labour - in the EV battery supply chain.
AI 'crucial' in battle for EV supply chain visibility
Bindiya Vakil is CEO and founder of Resilinc, the supply chain risk management specialist. Vakil says that, in today’s world, it is vital that organisations safeguard their supply, reputation, and bottom line, and that EV manufacturers in particular must ensure their associated supply network is as compliant as possible. Asked how EV makers can achieve supply chain visibility, Vakil says autonomous AI mapping and supplier-validated mapping are key.
“This provides deep insights into multi-tier supply networks, which is crucial to identifying which suppliers are operating in high-risk regions such as Xinjiang Uygur Autonomous Region, and how far down the supply chain this goes," she said. “This enables automakers to discover if there are any sanctioned suppliers in their network, at which point an alternative compliant supplier can be found."
As for assessing ESG risks, such as slave labour in the EV supply chain, she says recently introduced supply chain laws are forcing the issue here.
“With the introduction of the Uyghur Forced Labor Prevention Act (UFLPA) and Corporate sustainability due diligence (CSDDD), validating supply chains to ensure fair labour practices is quickly becoming a necessity. Given how interconnected auto supply chains are, these directives will certainly impact EV manufacturers outside the US and the EU too.”
ESG evaluations needed in EV battery supply chain
Vakil points out that this is why assessments, ESG evaluations and custom compliance assessments are crucial to building direct communication with suppliers, so that any violations or concerns can be addressed accordingly.
“Not only is this a more collaborative approach, but it is also a transparent and effective way to halt forced labour in supply chains,” she said.
Being able to shine a light on vulnerable suppliers in the EV value chain is another key area.
“Through using assessment scores to quantify the level of compliance from each supplier, automakers can better prioritise which suppliers are most vulnerable to forced labour violations,” she says. “Such suppliers are often found in the sub-tier levels of an automaker’s supply chain.”
Vakil adds that working with suppliers to reduce exposure to forced-labour issues demands that joint plans with suppliers are put in place.
“Such a plan should factor in training for workers, a plan for remediation if forced labour violations are identified and sanctions for suppliers that do not follow procedures,” she said. “Auto manufacturers should also provide guidance, resources, and support to suppliers who will in turn help to verify their products and materials are fully ESG compliant."
Active supplier monitoring is another factor in maintaining a clean EV supply chain.
“Tracking the progress of suppliers’ implemented mitigation plans is especially important if gaps in compliance are to be fully closed in the long-term,” says Vakil. “Active monitoring ensures EV manufacturers can verify that suppliers are maintaining compliant practices. Consistent communication and collaboration are fundamental to reducing any forced-labour risks in the long-term.”
*******************
Make sure you check out the latest edition of EV Magazine and also sign up to our global conference series - Sustainability LIVE 2024.
*******************
EV is a BizClik brand.